Power Failure in Our Industry!
Thursday, May 26, 2011
Once upon a time in the Chemical Reaction Engineering Research Laboratory
On a sweet Thursday afternoon (today) when I just started my experiment, a sudden power failure occurred without warning. I was actually in the toilet when the power cut off took place. My wife called and asked, "Do you have electricity there in the lab?". I answered, "We have power here in the lab and I just started my experiment". Then 2 lab assistants walk out from the polymer lab (which is next to the reaction engineering lab) and informed me that the power failure just happened. I was surprised.

After about 15 to 20 minutes the electrical power resumed. Thank God. I switched it on. I then checked the GC and its PC hoping that nothing will go wrong. When the power failure occurred just now, the oven temperature (of the GC) was 250oC. The standard operating procedure to switch off the GC is when the oven temperature is below 40oC. Sudden GC shut down is not recommended at all. It is strictly a big NO. Luckily the GC works well and nothing seems to be wrong. I restarted my experiment and completed it 3 hours later.
Power Failure in the Plant
The incident reminded me on the power failure that once in a while also occurred in the physical refinery plant I worked in several years ago. Such unavoidable power cut-off from the Electricity Company will firstly trigger chaos within the control room and the entire plant. The supervisor, shift leader and plant operators have to act fast to close all main valves manually from various sections. The flow, temperature and pressure from numerous unit operation equipment such as Niagara filter (filter leaves), deodoriser, packed column, heat exchanger need to be controlled until power resumed. The huge 3000 tonnes per day plant can only be minimally controlled via the PLC which was temporarily powered with UPS (uninterupted power supply) - which provided a few minutes power back up.

What can we do?
As for my case, in the lab... nothing much can be done. I rest my faith to the God. It's good to install UPS for the GC. If UPS is the answer, then we must have 4 UPS unit in the lab as there are all together 3 GC's and 1 GCMS. However, having UPS alone will not entirely protect this expansive machines. For me, the power company (electricity supplier) must be responsible in providing smooth and reliable power for us (the customers). They should pay all the damage and losses that hit us. Maybe this does not sound like an engineer's solution...
Other option?
A more interesting option is to create and manage our own power system...but can we do it with our resources? I'm referring to solar, wind and frequency (Tesla) energy. I would love to develop one of this power sources AFTER I complete my study. I'll try and do it at my home first... :)
.................................................................................................................................
FREE Recommended magazines to get you updated with current engineering news
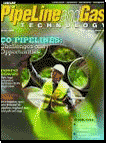
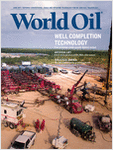
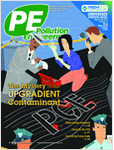
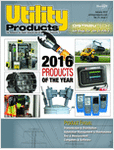
Have you downloaded my free "Choosing Alternative Fuel" Ebook? If not, then please download it here. It's Free and on top of getting the free ebook, you'll get eCourse on Alternative Fuel. It's a good and easy way to add more valuable information to yourself.
Image #1 credited to: http://www.wkow.com/Global/story.asp?S=14691294&clienttype=printable
Image #2 credited to: http://www.msnbc.msn.com/id/42761336/ns/us_news-life/t/refinery-warnings-way-life-texas-city/
Labels: Chemical Engineer, Chemical Engineering, Chemical Plant, Control System, Energy, Equipments, green, Learning Curve, Plant Shutdown, Problem, Process Parameters, Processing.
posted by Kipas Repair JB @ 7:54 PM,
0 Comments:
The Author

I’m Zaki. I used to be a project, process and chemical engineer. Few years ago I successfully became a Chartered Engineer (IChemE) and Professional Engineer (BEM). I'm now employed as a chemical engineering educator/researcher/consultant. Hope you like reading my blog. I welcome any feedback from you. My email: zaki.yz[alias]gmail.com. TQ!