My Intention....
When i first start writing in this site, my intention was to provide more information about the career as a chemical engineer and any career closely related to it. This is mainly because, i was also not sure what is chemical engineering....I did mention in my previous post something about how i have a very vague vision about the field of chemical engineering, but i decided to pursue a degree in this field because i like chemistry.
Therefore, i would like to give all information related to chemical engineering to future chemical engineering studets. I would also expose my experience as a practicing chemical engineer to those chemical engineering students, so that they will know more or less how and what does a chemical engineer do. What can they expect as a chemical engineer....and so on.... Maybe I'm not that old yet, and do not have that huge experiece in chemical engineering stuff, but i think i have tasted various fields of chemical engineering afer i completed my degree.
Well, after completed my chemical engineering degree from University of Bradford, I returned to my country, Malaysia. My original plan and my ambition is to become a lecturer. I began to work as a research assistant and continue my masters degree in chemical engineering specializing in Reaction Engineering - Catalysis Technology. So, i was there doing those research work for 2 years ++. My son -Maybe he wants to be a chemical engineer too. Following his parent's...
Then, after my masters degree i joined a local oil and gas service company. With this company i did a lot of specialty chemical stuff associated with oil and gas. I travel a lot doing projects here and there, onshore and offshore. It was really exciting, interesting and challenging. I've been with that company for about 2.5 years. I have to leave the company because it want to move to KL. I can't move because all my family and parents are here and we just purchased a house in johor bahru.
I move on with my life and got a job in an oil refinery in Johor Bahru. However, i have to commute daily for about 98km in order to go and return from work. This is another chapter of my chemical engineering career. This one was a challenging and interesting one as well. So, at the point i'm posting this story, i've been working in the refinery for about 1 year and 3 months now. But the amount of knowledge and information that is kept in my drive O inside my CPU brain is so much....Luckily RAM is also high......512 MB.....This photo was taken in the morning and i'm already sweating...
So, from my experiences that i gain all these years, i hope i can help few people who choose chemical engineering as a career some information and knowledge. I hope this can further and increase your comprehension on chemical engineering.
I'm also working on to create another page/site dedicated to the subject of heat exchanger, cooling tower, boiler, specialty chemical, instrumentaion + automation, oil and gas. However, i guess that will take some time to complete as i'm also working full time. I can only do this after work when i have the energy....
posted by Kipas Repair JB @ 8:23 PM,
,
Not My Typical Day As A Process Engineer...
A lot of things happen this week. To be exact...these 2 days.....
In the early hours today, electricity power was out. The whole factory was affected and the whole plant have to stopped. This was already a bad sign of the day....I guess....
Well, then we realised that it happened for a matter of seconds only. The power provider had changed the power station and unfortunately that resulted the power to be not available for 2 - 3 seconds. The effect to my plant was a massive downtime.
During this sudden power breakdown, many pending maintenance job that could not be performed during normal plant operation was carried out. But, the timing must be monitored. If the maintenance work took a lots of time, and the time to regain power is less, then the maintenace work should not be carried out. However, if the work requires less time, then it might be possible to decide on doing the job fasttttt........So, this is the point where decision making is vital.
My colleague install the UPS system (a power back up system) for the PLC (programable logic controler) in my plant. The process took about 45 minutes. They cannot install the UPS during normal plant running hour because to install the UPS, the PLC must be switched off (the plant is running 24 hours). So, when the plant is down, it was a fantastic opportunity to install UPS.
As soon as the power returned, the plant supervisor and operator were very busy doing their job starting up the plant. Many sections need to be handled and be taken care off. The vacuum system need to be stabilized. The high pressure boiler need to be switched on and obtain the desired pressure to reach targeted temperature. The cooling tower need to be in great shape to supply water to plant to establish good vacuum.
Unfortunately, one of the cooling tower fan was broken when the plant attempted to start up. So, we cannot use that cooling tower. We have to use another cooling tower which was under cleaning. Luckily, cell no 1 of the cooling tower which is under cleaning is ready for duty....However, the 12" gate valve on top of that cooling tower is leaking and have to be replaced with a new one in order to make the cooling tower work. Another 1.5 hours there.....Soon, a 20 tonne crane entered the plant and lifted the damaged fan down for maintenance. The 8 bladed fan was serviced, repaired and fixed backed to its original position.
At the same time, during this starting up of plant, many unexpected thing can also happen. This is one of the most critical part of running a plant. Any careless mistake can lead to a devastating catrostrophy. One of the vessel was caught on fire. Luckily, it was detected fast and everything was under control.
Then, when we tought that everything was going to be ok, suddenly the power was cut-off again (for the second time within just 3 hours from the first one). I immedietly called the chargeman and asked him to check out and rectify the problem. Well, it was not only a problem for my plant, but also the whole plant in the factory again, which now it include the boiler. This cannot be good. And this happened nearby lunch time. I get myself some update of what really when wrong by visiting the LV room. Well, it was found that the main fius switch for all the plant was totally wipe out!!! It look really "cool" in black!!!! well, it burnt....and nearly became like coal... Estimated time to fix the mess was 2 hours. So, just wait for another 2 hours and we did some other maintenance work that can be done while the power is gone...
After 2 hours, the power returned. Now, another problem appeared. The boiler cannot be started because its transformer suddenly cannot work. That piece of plastic + metal need to be replaced. After that, the boiler can be started and steam is delivered to respective plants with sufficient pressure.
At the same moment, I must make myself available for an appointment which was arranged a week earlier with a supplier who came from KL. We were discussing some stuff about networking, IT and some PLC conection matter....This is already another big subject....The problem now, I was called for a sudden big meeting with HQ...Oh no!!!....What now? I have to inform my senior that i cannot join the meeting. I have to discuss something with this supplier. We already had an appointment.
Earlier before lunch, i was called to attend the daily production meeting. Usually my senior will attend the meeting, but on this day, some visitor from some country came and he have to lead the tour guide in the plant. So, there i go for the meeting....of course i've been asked few things about wether my plant can run the type of oil that some customer requested....when? tomorrow!!! Ok.....this is not normal process. We have not run this oil before, so i cannot answer....I must refer to my senior exec and senior supervisor to check on the feasibility of the process.
Another project that i handle which is the tank gauging experience some communication problems. However, the power problem unexpectedly made the communication to improve and the system became ok. As i prepare myself to go home, i notice that the earlier tank gauging problem came back....Oh no....I shook my head disbelief....it's happening again...
Well....all of this happened in a one very long day today.....and always when i reached home, it's already dark....i cannot event see my flowers bloom during daylight because i always reach home when it's already dark....Luckily tomorrow is a public holiday....huh...!!!
posted by Kipas Repair JB @ 8:40 PM,
,
BIODIESEL BASICS II
There a lot more to learn and study and explore about this biodiesel subjects. One of my source of information is the Oil and Fats International magazine published by DNG, UK. Actually, the magazine covers all about news, technologies, information, advertisement, announcement related to oils and fats internationally. Well, biodiesel is part of this subject as well. Below is an article that i would like to share regarding biodiesel in the west, which i read recently...from the magazine....
News Article ID: 1123109 June 2006
Fuel Speed Ahead: Biodiesel Gains Record Momentum
Peter LaVaute says people know him as an environmentalist. But he's also a businessman who looks for lucrative opportunities, and he's hoping to build multiple biodiesel plants. LaVaute is part of a trend that some have likened to a gold rush. Jenna Higgins writes.
"I believe we're about to run into a brick wall - lack of fossil fuel," he said. "As a country, we're going to have to change the way we provide goods and services. We're going to have no choice but to become self-sufficient."
LaVaute, president of Ecosense Solutions, sees biodiesel as one of the most promising opportunities to fill a growing need for domestic fuel. He also sees it as a chance to help with something else that is important to him - revitalising rural communities. One of his biodiesel projects involves working with farmers in central Nebraska on developing a multi-feedstock biodiesel plant. In addition to the more typical soybean oil feedstock, the plant could make biodiesel from sunflower oil.
"One of the most exciting things to me is to develop a resource a community has, but has overlooked," he said. Sunflower seeds are 40-50% oil, he said, and the crop is relatively low-input and drought resistant.
For now, LaVaute's Nebraska biodiesel plant is just the seed of an idea. But he is among a growing number of entrepreneurs with biodiesel projects on the drawing board.
The National Biodiesel Board (NBB) estimates there are 30 plants currently in the early planning stages. Another 45 are already under construction. Compare that to the number of plants already operating, 60, and it's easy to see how fast the industry is growing.
"I take about 25 calls per day from people interested in starting biodiesel plants," said Donnell Rehagen, NBB's chief operating officer. "Frankly, the pace of the growth is sometimes startling. We hope we don't see empty biodiesel plants in five years, but that's for market forces to determine. It's unlikely that everyone will succeed."
Read the full story in Oils and Fats International July 06. You can read or subscribe the "Oil and Fats Magazine" at >>> http://www.oilsandfatsinternational.com/default.asp?pubid=28&nav=0
For other reading material and information about biodiesel...go to the these links....
http://www.mosta.org.my/events/6_Programme.pdf ---> Oils and Fats International & Malaysian Oil Scientiest and Technologist Association (MOSTA) is organizing Oils and Fats International Congress 2006 (OFIC 2006)Incorporating Oils and Fats International Asia 2006 (formerly OFTEX). Get more details from this link....I'm also going to this exhibition in September in Kuala Lumpur. Don't worry, I'll get the information posted after my visit there....
http://www.biodiesel.org ---> National Biodiesel Board
http://www.biodieselgear.com/---> Some technical info about Biodiesel
http://www.biodieselnow.com ---> Can discuss & exchange ideas in Biodiesel forum
posted by Kipas Repair JB @ 12:01 AM,
,
Hi! I just stop a while telling my experience as a chemical engineering student. If i keep on writting about that, then i guess everybody will get bored. So, I will alternate my post....something a little technical and some of my experiences....
BIODIESEL BASICS I....
Since the biodiesel concept was introduced sometime ago, many researches were carried out to study the feasibility of this spectacular idea. Some countries in Europe has already attempted and succesfully implemented the biodiesel technology. My country, Malaysia has also indulged in the research activities and is now actively encouranging private sectors and palm oil company to develop biodiesel plant.
Now, the phrase "biodiesel" can be heard anywhere and everwhere in this industry. What is so great about biodiesel? What is Biodiesel? How is it made? From my interaction with some people, many do not understand what actaully is biodiesel.....I'll briefly explain about biodiesel...in this post and also in the coming post....
What is biodiesel?
Biodiesel is the name of a clean burning alternative fuel, produced from domestic, renewable resources. Biodiesel contains no petroleum, but it can be blended at any level with petroleum diesel to create a biodiesel blend. It can be used in compression-ignition (diesel) engines with little or no modifications. Biodiesel is simple to use, biodegradable, nontoxic, and essentially free of sulfur and aromatics.
How is biodiesel made?
Biodiesel is made through a chemical process called transesterification whereby the glycerin is separated from the fat or vegetable oil. The process leaves behind two products -- methyl esters (the chemical name for biodiesel) and glycerin (a valuable byproduct usually sold to be used in soaps and other products).
Let's continue later.....in my next posts.....
posted by Kipas Repair JB @ 12:15 AM,
,
Mid Chapter as A Chemical Engineering Student
It was a very exciting feeling to start a new semester in a new place in another country with a totally different background. The plan now is to study chemical engineering for 4 semesters (3, 4, 5 & 6), and after that get the chemical engineering degree. The subjects that i took for all those semesters were:
Semester 3 & 4:
1. Mass Transfer
2. Heat Transfer
3. Fluid Mechanics
4. Process Control
5. Foundations of Accounting
6. English Language
7. Process Design
8. Computer Aided Process Engineering
9. Process Safety
10. Powder Technology
11. Mixing Processes
12. Advance Control
Semester 5 & 6:
1. Differential Mass Transfer
2. Fuild and Particle Mechanics
3. Reaction Engineering
4. Process Control & Instrumentation
5. Applied Chemical Thermodynamics
6. Quality Engineering
7. Biochemical Engineering
8. Non-Newtonian Fluid
9. Business Strategy
10. Design Project - Alumina from Bauxite
posted by Kipas Repair JB @ 1:04 AM,
,
Mid Chapter of A Chemical Engineering Student
One of my proudest moment was when i successfully get myself a place to study chemical engineering in UK. I can remember how proud my parents were, especially my father. I'm glad to make them happy. The day came and all of us, the JPA (government) sponsored student gathered at the Kuala Lumpur International Airport (KLIA) that evening. All my family members were at the airport to wish goodbye and good luck. We (myself and my colleague) were very excited at this moment. We were really looking forward to enjoy the journey. Some of us have never been on a plane. So, these category of people were more excited + a little bit suspen!!!
Bradford city Hall
The journey took about +/-12 hours by the MAS 747-400, and we really enjoyed the journey. We had some sleep and ate some nice food served to us. We arrived at Heatrow Airport on the following morning. The temperature was very cool (autumn) and the wind was blowing strong (maybe 30 kPa + +....hi hi...or 90 miles/hr). And yes we came prepared with all these winter clothing. We transited at London and took a Focker-28 to Leeds-Bradford airport. It was a smaller plane with a pair of engine. I don't know what type of engine...Definitely not a Rolls Royce engine.....The wind turbulence was very fierce that time. The plane seems to be drifting up and down, left to right to left again....some of us lost the appetite to eat the delicious croissant and orange juice served to us. But most importantly, the aircraft landed safely and we went out of the fiuslaj in one piece...breathing fresh midland air....and it's a very cold one...
Bradford Interchange
Some mature student (post graduate) have waited for our arrival and they picked us to their home. They tell us all the basic information and what we should know about the life in Bradford: how to eat, what to eat, where to buy food, where to shop, how to adopt, the bank location, the post office location, and other vital informations that we really need in this new place....I stayed in a post graduate's house whom i called Abang Hilmi, with another 2 friends. It was just a temporary home before we can get a house to rent. After we managed to get a decent small 3 storey terrace house + a basement in the Bradford city (12, Noble Street, BD7 3BD), we moved in. It was a very cold house without any central heating....and it cost us 250 pounds per month. That's very cheap for a house...and a freezing one. The four of us occupied the house and we split the 250 by 4. The land lord, a Pakistani British citizen live next to the property and never misses to ask for the rent on the 1st of everymonth!!! .....Next....starting a new chapter as a foreign student.......
posted by Kipas Repair JB @ 10:37 PM,
,
Early Chapter as a Chemical Engineering Student II
In the Nothern Consort ium United Kingdom (NCUK) program, the life is not as easy as expected. I'm now a first year chemical engineering student. I have to learn more chemical engineering subjects. It was simply because NCUK is a program for first year university that uses the syllabus for a number of universitis offering chemical engineering degree in the Midlands, UK. So, instead of learning first year subjects of a university, i have to learn subjects from a combination of university, which means I have to slightly learn more. Well, all university offering chemical engineering will have a in general a quite similar basic first year subjects. So, well....that's ok. I have to face it.
The subjects that i learned during that first year university:
1. Chemical & Power Thermodynamic
2. Material & Energy Balance
3. Unit Operations - I realised i applied a lot of this in work now....
4. Fluid Flow, Heat & Mass Transfer - I used the knowledge of this as well in plant
5. Strength of Material
6. Reaction Kinetics
7. Engineering Drawings - I like this...because i like drawing...
8. Engineering Mathematics/Statistics - I didn't like this...all the differentiation and calculus!!!
9. Laboratory Experiments - Lots of very interesting experiments and it's fun!!!
10. First Year Design Project - could not really remember...about this....
Well, at the end of year, i took the exams together with the rest of my friends. It's so tough!!! It was the most difficult examinations that i have ever taken in my entire life....This exam was very critical as it decides wether you go to UK or you stay in the country....I can recalled some of my friends crying while answering the examination papers. I can also see my friends shaking their head not knowing what to answer. All papers were veryyyy tough, but the most cruel and disastrous were Unit Operation and Engineering Maths. The lecturer, to my suprised enjoyed seing us cannot answer the questions....Oh no....what will our future be?? That questions linger in most of our heart....Are we going to UK or not?
The day came and the result was released. It's now a matter of "pass" OR "fail"...Everybody were worried. Worried that they won't make it for UK. Well, to my relieve, i passed the first year examination. Majority of my friends passed too. If I'm not mistaken, maybe about 10 of my friends failed and they were very miserable. I felt sorry for them. Life goes on...and now I'm on my way to UK..........I believe I can fly.....
posted by Kipas Repair JB @ 8:44 PM,
,
Early Chapter as a Chemical Engineering Student
When I decided to study chemical engineering long ago, i did not really know about the course. I fancy chemistry, and that directed me to chemical engineering. That time the internet is still not there, or perhaps very very new to human beings....So, without really knowing what the hell is chemical engineering, i just took the course. Applied the program from the local education ministry, get myself and interview for a schorlarship/loan....And there I'm on my way to become a chemical engineer...which i still don't really know about it.
So, I started the early chapter as a chemical engineering student by entering the A-Level program at Institute Teknologi Mara, Centre of Preparatory Education. It's basically a twinning program between the Malaysian government and the United Kingdom's. The plan was, to do the A-Level for 2 year, another year of first year university at the "Nothern Consortium United Kingdom" (NCUK) [still in Malaysia], and then if we passed our first year, we shall proceed to universities in the UK for another 2 years.
Well, A-Level is supposed to be 2 years. But in actual, the REAL A-Level was 1.5 years. The other 0.5 year, which was the first 6 months of the 2 years, was just pure English study, comprehension, speaking, writting etc. Well, this is to really prepare ourself to be proficient in English when we go to UK. So, after that 6 months I started learning those 3 basic subjects: Physics, Chemistry and Mathematics. Well, there's definitely some practical lesson/lab for physics and chemistry. For maths, we studied pure maths and mechanics...Don't ask me now, I forgot all those stuff....So, now the objective is to score good result in the A-Level program so that we can go to good decent university in UK. Well, to make it short, I get average result for my A-Levels. And i manage to get myself a place in Bradford University, in the Midland of Britain. But first, i have to complete and pass the NCUK before going to UK....to be continued....
posted by Kipas Repair JB @ 10:11 PM,
,
High Pressure Boiler in Plant
For any plant that requires such a high temperatue in their process system, they need a high pressure boiler. This high pressure boiler can provide you the high temperature that your plants according to your plant demand. However, operating and maintaining the high pressure boiler is not something simple. It requires some knowledge and some experience as well. For me, I still need to learn more about the high pressure boiler. I also need to have more practical exposure on how to start, trouble shoot and operate the high pressure boiler. Well, for now, i do know a little about the high pressure boiler. A friend of mine, yesterday, asked me about his problem on operating a high pressure boiler. The following is his email to me.....
"How are U? ..
Hey, check with u something, have u experience that your High Pressure Boiler in your plant trip due to low water level? As I know it is a closed system where all the water vaporize to steam and condense into condensate in the system. At my place here, the HP boiler trip due to water low level. But, they cannot find the leakages...."
Well, what my friend is facing sometimes happen in any plant using a high pressure boiler. When there is some water loss from the high pressure boiler and its close system, there's definitely a leakage somewhere. You need to search, find the leaking point. Get some more help. Get more people searching for the leaking point. Do a steam test to easily detect the leak. When you find the leak, close the leak point. Well this depends on how bad/how big/small the leaking point is. Just rectify the problem, and make sure there's no more leak inside your high pressure close system. When there's no leak, water loss would not happen. The water will just follow its cycle from being a steam, then condensate, and steam again, and condensate again, and so on...without dissapering....
Note...I'm not really a high pressure boiler expert. I also need to learn some more....
posted by Kipas Repair JB @ 3:53 PM,
,
AUTO TANK GAUGING PROJECT
One of my task as a process engineer is to lead/handle the "Auto Tank Gauging" (ATG) project. It's a project that is very chalenging. I face a lot of obstacles that i have expected and also that i never expected. What is this ATG project? Let me brief about it....
There are a number of oil storage tanks at the plant/factory that i work in. Every morning, the operation department/pump house boys will do the manual dipping / ulleging to measure the oil level inside the tank. From this, operation can know the stock of the oil. The process is so far ok and the oil level readings are fine.
However, in order to constantly monitor and know the oil level and tonnage of oil inside the storage tank, ATG is introduced. It will basically measure the level of oil inside the tank using micro pilot radar / ultrasonic wavelenght and/or using level probe. By using this instrument, simply said, we can see the oil levels inside the pc that is connected to the instrument at the tank. Besides the instrument to detect the level, temperature transmitter is also installed. This is vital to measure the temperature of oil at all time. The temperature will affect the density of oil. By knowing the oil level (height), we can get the volume of oil inside the tank. Having the volume of oil multiplied by the oil density, we can get the tonnage. The tonnage is the most crucial information for the daily oil stock.
The whole process of installing the instrument, laying cable, dealing with suppliers/contractors, commisioning, trouble shooting problems are tough. It really requires a very good coordination. Not many of my chemical engineering knowledge is put on practice while handling this project. It's more towards managing and also learning some SCADA system program, monitoring the tanks and also fine tuning the instrument to get better accuracy.
I experienced a lot of technical problem while handling this project. The lists of problems are so long that i think i cannot write it here now. Perhaps later on. I think it's good to share the experience to others when the time comes. Went the project is totally completed....
For more info or some ATG reading material, click here
posted by Kipas Repair JB @ 9:14 PM,
,
CHEMICAL ENGINEERING - CHEMICAL BLENDING
When i was working in my previous company, doing some oil and gas business, I did mentioned that we take care of some pipelines which contain condensate and gas. The pipelines are quite long, several kilometres. We have to maintain the pipelines from corrosion damage. Therefore, we have to select some specialty chemicals such as degreaser and also corrosion inhibitor, to be injected in the pipeline.
The degreaser main purpose is to provide enough alkaline so that any debris or sludge deposited in the pipeline can be easily remove by using the bi-directional pig.
The corrosion inhibitor which is an alkyl ammine base (Quartenary pyridine alkyl ammonium), a water base concentrate will create a thin layer layer on the internal side of the pipeline to protect from any corrosion to develop. After injecting the corrosion inhibitor, a filment pig will evenly distribute the chemical onto the internal pipeline section.
The condensate pipeline is a 10" diameter pipeline whereas the gas pipeline has a diameter of 48". So, can you imagine how big is the bi-di pig and the filment pig for the gas pipeline?!!! The weight of each 48" pig is 2 tonnes. It's not an easy job to to do the pigging job for the gas pipeline.
However, the challenging task for me was to prepare and blend the chemicals to be injected inside the pipeline. It's a very tough job too. I have to blend degreaser up to 15 m3 and corrosion inhibitor up to 3 m3. It's a lot amount of chemicals to be blend using just some 2.7 m3 poly tank. I have to coordinate all the blending process, manage the transportation of water, be aware of the timing and also supervising the process of injecting the chemicals into the pipeline. But, the most important task is to ensure the chemical's quality. I have to conduct several tests before allowing the chemical to be dosed into the pipeline. I have to conduct compatibility test, foaming test, emulsion test and few other tests. If the test failed, i have to adjust the chemical blending accordingly until the quality is obtained. All of these chemical blending process takes place at site under a very hot sun!!! Imagine working under the sun wearing the nomex and tyvek coverall (i did mention about the safety coverall in my previous post). Uhhh...it's damn hot....Just imagine that i can easily drink and finish the 500ml mineral water bottle in 8 seconds!!! Yeahh...it's that hot....
Get the Weatherford specialty chemical (corrosion inhibitor) information that i used while doing this projet here
posted by Kipas Repair JB @ 8:02 PM,
,
Doing Chemical Engineering Research
While doing a Chemical Engineering Degree, besides learning all the Fundamental of Chemical Engineering subjects, we have some design project to deal with. Doing the design project is very interesting as we really put ourself as a chemical engineer, thinking of how to commercialise certain project, when to get the Return on Investment (ROI), doing some autocad drawing of the plant, selecting which process and equipment to purchase etc. Some other chemical engineering students in some other university will do a small research work. This is actually a very good exposure for the undergraduate students on how to do research work. Normally the students will be allocated a few weeks or perhaps 1-2 semester to complete their small thesis/dissertation. Some can do the research with few obstacles from the experiment etc. Some could not continue doing those research or be in a very advance research group which always stresses for results.
For me, after my undergraduate study, I continued with Masters in Chemical Engineering. I did a full time research study in Universiti Teknologi Malaysia supervised by Prof. Dr. Nor Aishah Saidina Amin, a very successful researcher. The research is actually about converting natural gas into gasoline via a single step process using modified zeolite catalyst. It was a very interesting research. I explored and learn a lot while doing the research. We synthesized and modified the zeolite catalysts ourself. We characterized the catalyst using various instruments such as X-Ray Diffraction (XRD), Scanning Electron Microscopy (SEM), Fourier Transform Infra Red (FTIR), Temperature Program Desorption (TPD) etc.
So, after satisfied with the quality of the catalyst, we tested them in our self made experimental rig. The experiment normally took slightly more than 8 hours. At the end of the experiment, we hope to get some amount of liquid/oil/gasoline. This liquid will be analyzed in a Gas chromatography to check its hydrocarbon composition. As fas as i can remember, we tested the Research Octane Number (RON), and the best that we have ever obtained is 88 (Dr./Pak Didi (my good research friend): correct me if I'm wrong)...Well....this outstanding research have won us numerous awards and recognitions. That was the main research in the Chemical Reaction Engineering Group. My research was investigating the reaction of converting methane(CH4) which is the main component of natural gas into ethane(C2H6)/ethylene(C2H4) via the the production of methyl radical (CH3*). This reaction will only occur with the presence of metal oxide catalyst and temperature of about 700 - 850 celcius. Well, i felt it was a very good research and experience. I did faced so many obstacles along the way. Luckily, a new friend that suddenly appeared, helped me and shared some ideas on completing the research- special thanks to Pak Tutuk.
I could also not forget the companion of Pidun whom was doing the Palm oil to gasoline process. Also Sean, Istadi, Kusmiyai, Rozi, K ida and the rest....But, the most support came from my beloved wife, Mazura who supported me all the way. Well....thank god, it's over....However, I deep inside I fancy to do a PhD in Chemica Engineering. Well, my wife is in her first year of doing her PhD...Also Chemical Engineering > Separation > Crystallization....
posted by Kipas Repair JB @ 8:17 PM,
,
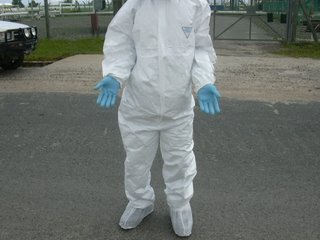
So, there we go, do our work...wearing all the safety helmet, safety goggles, Tyvek coverall (protecting from chemicals/oils/condensate), Safety boot, rubber glove + cotton glove. Well, after some time doing the work using those PPE, there were findings that the oil/condensate that we sometimes play around with....contain some amount of mercury....So, guess what, the regulation became more strict....Then, we have to discuss things more detail inside the meeting/pre-job meeting to overcome the hazard from mercury. Some additional steps/precaution have to be taken. In addition to that, it was also discovered, that the flash point of the condensate that we face during work may cause ignite fire (or worse...explode)...so, again addional discussion...bla...bla..and more precaution...more PPE.....
So, finally it was concluded that we have to wear 2 coveralls at one time during work, one is NOMEX - a fire proof coverall..which can protect us for getting enough time to escape if we are caught in fire......and the second one...is some Tyvek coverall that is mercury/heavy metal proof....Ooohhh could you imagine wearing 2 coveralls under the hot sun while doing our pipeline maintaince work....
Not only that, we have to wear 3M full face piece with mercury filter - 6009 and also organic gas filter 6003....OOooo man...it's damn hot inside there...I'm sweating like ##$%%*!##? it's very hottt..
Anyway...that does not stop there...There're more things to tell you about what we have to face with the mercury issue around....I'll post about it later in future....just wait...
posted by Kipas Repair JB @ 9:41 PM,
,
3D Trasar - The Cooling Tower Might be Coo00ool with it...
As I mentioned in my post earlier, handling a cooling tower might not be that cool if the coling tower is creating so much problem from so many angles. The problem in cooling tower triggered from other sources will create massive operational and process problem. Operating costs will also increase. Maintenance costs would also be definitely there in the calculation. You would not want your cooling tower to have a very deviating pH. You also don't want your cooling tower to have so many Legionella bacteria cultivating inside the cooling tower splash bars. And you don't want any chemistry to be not right in the cooling tower. You want your cooling tower to be in a tip top condition, providing desired temperature for the process plant.
Most of the current and previous method is based on the "dose and hope for the best system" which means the chemical supplier comes and do some tehcnical checking/evaluation of your cooling tower. Testing some water parameters, take down some notes and provide you with some black and white report. The question is how frequent will he do this? Once a week? once a fortnight? Who knows what's the water quality when nobody is checking it in between those supplier visit?!! What about the lab? Is the lab checking the quality on daily basis? If yes, what about the interval between those lab sample testing? Perhaps your cooling tower is slowly deterirating and suffering from some "alien" atack!!!
How to overcome this??? Well, earlier this year i knew that Nalco have come out with their secret weopen in having a better control of the cooling tower. Nalco took few years to develop the best control system to overcome stresses inside the cooling tower. They develop 3D Trasar, a tool to monitor dan have better control of the cooling tower. It's simply a very good and impressive invention. Presently, many company already installed the 3D Trasar inside their cooling tower. And one good thing about 3D Trasar....you can monitor and control the cooling tower from anywhere in the globe. Enough about that, I'm not the expert of this 3D Trasar...You better get further information from Nalco. Alternatively you can click this link Read more about 3D Trasar
Learn more about 3D Trasar Applications
posted by Kipas Repair JB @ 3:19 PM,
,
What You Don't Learn About Plate Heat Exchanger in Uni....
For those chemical engineers who're new, or chemical engineering students, or chemical engineers who have not yet experience dealing or operating a plate heat exchanger, well, this plate heat exchager (PHE) is not as simple as what we see in those any heat transfer text book or Perrys.
Nobody teaches you how to take care, operate, change plates, change gasket of the PHE. You don't get this information in the text book. The text book only have some theory and example of calculating the overall heat transfer coefficient, Log mean temperature difference (LMTD) and few other formulas.... You'll ONLY get the knowledge went you deal with it, or learn it from your senior engineer, or from your supervisor or fitters/technician. We were also not thought of how long is the life spent of the PHE?! How long is the time where the PHE can work with highest efficiency of doing its' main job of tranfering heat between two liquids?? How many plates are we supposed to allocate for a heat exchager?? We never learn all those stuff in university....We learn them went we deal with them....It's quite difficult to discuss about the operation and other related issues regarding the PHE. It will be a long discussion. Later in future, i'll keep on posting slowly related issues regarding the PHE.
The most basic thing about PHE is that we want to "exchange heat"....We want some cold fluid to reach certain desired temperature higher than before and some hot fluid to reach a lower designated temperature. Well, sometimes you don't get the desired temperature too. Well...many reasons for that...check the flow rate....the flowrate affects the final temperature....Check the fouling at the plate and frame....is it serious....is the heat exchange efficient....?? Huhhh...lot's of thing to put here....but let me post them later on....enough info for today...ok...
posted by Kipas Repair JB @ 7:06 PM,
,
Pipeline Maintenance
Take care of your pipelines properly. Give them a good care. Never ignore them if something out of ordinary occurs.
Previously, i have a job of just taking a good care of pipelines. Why we have to take care of these pipelines? Why some oil and gas companies will invest a lot on taking care of their pipelines? Well, it's simple....these pipelines transport very precious thing....ie. oils..and also gases... So, we want to protect the products.
Then, the next reason is that it is not cheap to construct and lay a pipeline, especially for a very huge distance...Therefore, we want to really protect the asset (the pipeline). We don't want to keep on constructing the pipeline after a just 5-6 years of constructing them.
Well, i helped handling the pigging activity in some pipeline covering a distance of about 14 km. The main pigging activity is to create/put film of corrosion inhibitor into the internal part of the pipeline. This is to protect the pipeline from corrosion developing. Before injecting the corrosion inhibitor with the filming pig, we have to inject the pipeline with some amount and some concentration of degreaser, to remove any debris to scrap of some unwanted physical material trap inside the pipeline. Well, selecting the pigs and also the chemical is critical. I'll discuss about them in future, later on....wait for them....
posted by Kipas Repair JB @ 8:04 PM,
,
What is Chemical Engineering?
Our modern society relies on the work of Chemical Engineers – they help manage resources, protect the environment and control health and safety procedures, while developing the processes that make the products we desire or depend on.
Chemical Engineering is all about changing raw materials into useful products you use everyday in a safe and cost effective way. For example petrol, plastics and synthetic fibres such as polyester and nylon, all come from oil.
Chemical Engineers understand how to alter the chemical, biochemical or physical state of a substance, to create everything from face creams to fuels.
Biochemical Engineering, a more recent offshoot of Chemical Engineering, uses the very latest technology to produce pharmaceuticals and foods.
posted by Kipas Repair JB @ 11:35 PM,
,
Studying Chemical Engineering VS Practicing Chemical Engineering
In those early days, not so long ago, just few years back....we learned all these chemical engineering subjects: Thermodynamic, Reaction Engineering, Unit Operation, Strength of Material, Reaction Kinetics, Mass Balance, Heat & Mass Transfer, Process Control & Instrumentation, Advance Control, Powder Technology, Mixing, Fluid Mechanics .....etc...the lists continues.....
Well, i don't know about the others, but for me, i don't really 100% understand those subject. Well, the Prof/Dr/Lecturer lectures infront of the hall/room, and we tried our best (for them who really pay attention) to focus and absorb the theory of the subject. Attempted some questions to further establish the comprehension of the subjects. I recalled at one class, while Prof Walls was lecturing Heat Transfer, but always facing the white board, this naughty british lad creatively played with fire in the class!!! It was quite a scene ...but the Prof keep on bubbling and facing the white board....a very clear indication of a very boring class....well, boring for them, but for some asian student and some european student, they were focused.
I scored the highest mark in my "Computer Aided Process Engineering (CAPE)" under Dr Iqbal Mujtaba, a subject for semester 3, which later on the department awarded me the BP computing award that year. Well, what i received is just a gas handbook, not a certificate. However, that's not the point. The point is i get the highest mark, but, frankly speaking, i don't really understand the subject!!! And also what is Process control & Instrumentation, Advance control?!!! That time, i don't know.....but now...after sometime working...i realised and slowly understand what i learned previously. Oooo this is this, and that is that...oooo this is actually a rotary drum filter, why can't i imagined this when i was doing my final year design project?!!! Ooo that's why we need
posted by Kipas Repair JB @ 9:54 PM,
,
Some Maintenance Job During a very Short Shutdown
Sometimes, we have to face the fact that a sudden plant shutdown is unavoidable. It maybe because of some stupid but valid reason. Some repair work have to be done.... some additional piping must be carried out to improve the process system. Well, the list continues...You know, during shutdown, all jobs that can only be performed when the plant stop will be rushed.
You can also share your experience here.
posted by Kipas Repair JB @ 8:51 PM,
,
Plant Shut Down - The time to explore
During my first plant shutdown, i learned lots of new things. My learning curve suddenly increased. My understanding on this plant became better and better.
I know some other people have their own experiences dealing with this shut down. Well, during this time, all of us, technician, fitters, maintenance people, production people, operators, contract worker/helpers will combine and work together to repair/clean/rectify any problems. Some leaked valves will be replaced. Some identified cracking pipes will be either be replaced or welded. Maybe some heat exchanger need some RTD or temperature sensor to be installed upstream and downstream. One or two heat exchangers that don't have it's substitute might also be serviced. The list continues of shut down jobs continues...too long to list it here....
During this period, i took advantage of getting inside some of the vessels. I traveled deep inside all vessels that was possible for me to enter. It was hot and dark....need some fan ventilation to help us inhail. We checked the condition inside the pack column, deodoriser etc. It's dirty and oily and slippery. Imagine the temperature inside this vessel when it is in operation - 260 Celcius or more....uhhh that's pretty hot inside.
Well, the shutdown is some activity which is out of our daily routine job that improve our comprehension of the plant processes. What do you think?
posted by Kipas Repair JB @ 9:02 PM,
,
Cooling Tower is sometimes not that "co0000ol".....
Handling cooling tower when it's ok is such a great feeling. Knowing how to balance between the operational, mechanical and water chemistry is what we want, and when the cooling tower water produces the sort of desired temperature, well, and water quality is ok, everything should be in control.
But what happen when suddenly everything is out of control. When the water quality is worsening, turning brownish or greyish...or whatever colour you can mention it. When all heat transfer in you heat exchanger is no longer operating at its best capacity due to uneffectiveness of the heat transfer - "fauling" or other reasons. When your chiller get choked!!! Suddenly the cooling tower is deteriorating as well. All sort of greyish slimmy thing appeared sticking on the infills. The look of your cooling tower at this point is tremendously horrifying. At this point, the water in your cooling tower basin is producing unwanted blackish foam. The sand filter is sunddenly choked in a very short time. Back washed?!!! how long...no matter how long you back wash, the balckish, greyish colour water keep pouring out from the 3" mild steel pipe of you sand filter. What the hell is this??!!! This is not what i want!!! Oh man....my boss is going to screw me up.
The pump is delivering lower flowrate then usual when you check the flowrate. Oh no....my vacuum system is on its neck!!! Oh no my final oil product is too hot to be stored in the storage tank. Everything is not right at the moment.
Now, who's fault is this? The supervisor? the plant operators? the utility engineer? production exec? or is it me? Who? You keep shouting to youself deep inside. Oh no!!! Is it the water treatment chemical contributing to this disaster? Do some WHY-WHY analysis to outsource its origin....your headace is skyrocketing exponentially suddenly....Some oil might be leaking in some heat exchanger or chiller?? But which one? from which plant? Or no...this is totally a complete combination of disaster....
Suddenly your cooling tower is under stress!!! Settle the problem....How? Go and check all your lines from cooling tower....check all you heat exchangers.....check everything....something is totally penetrating the cooling water line....Do the air test, hydro test....take some sample from all the water inlet and outlet of your heat exchangers....chillers....check which one has the highest concentration of oil....
Damn this hydrocarbon....constantly feeding simoneela filming bacteria sticking on the internal wall and the entire cooling tower infills. And the search for the leaking point continues....and its not easy.....keep on searching.....GOOD LUCK....
Maybe you want to share some cool experience of your cooling tower???
posted by Kipas Repair JB @ 7:43 PM,
,
The Author

I’m Zaki. I used to be a project, process and chemical engineer. Few years ago I successfully became a Chartered Engineer (IChemE) and Professional Engineer (BEM). I'm now employed as a chemical engineering educator/researcher/consultant. Hope you like reading my blog. I welcome any feedback from you. My email: zaki.yz[alias]gmail.com. TQ!